
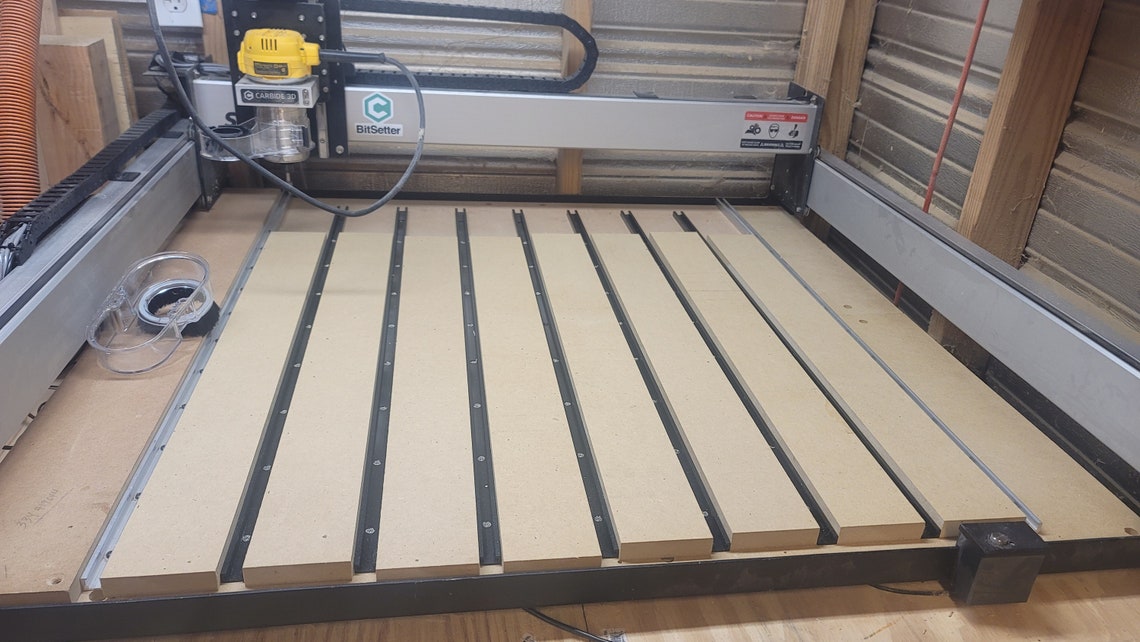
The 2mm endmill did a fantastic job pocketing out the void around the wrench. My contour operation failed, so I abandoned this project for now The savings in machine time and my own time means it will be a worthwhile purchase!
#Shapeoko xxl software
I need to invest in software that will do this for me. That way you could create a toolpath using the 2mm endmill that avoids that area. You could make another SVG with lines covering the area that would have been hogged out on the first pass with the big ¼” endmill. It would be possible to simulate this with Carbide Create. For this to work well, your CAM software needs to be aware of the material that was already removed on the previous pass. This would save a lot of time, but I don’t think I can do this efficiently with Carbide Create. Today’s estimate was another three hours, so this is definitely going slower!Ĭan you use a bigger endmill to remove most of the material? I did my best to pick up right around where I left off, so there was 0.9mm left to pocket out. I started today with roughly 0.6mm already pocketed out, and I had set the depth of that pocket to 1.5mm. The second endmill broke after an hour of cutting. With last night’s settings, the job was going to take about three hours. These are the settings I’m using successfully right now: That must be acceptable when cutting MDF, but it was killing my mills when cutting aluminum! I lowered the stepover to 0.8mm, and it seems to be doing a much better job. I left it at Carbide Create’s default of 1.4mm. Where did I goof? I goofed up the stepover. I attempted to pick up the job roughly where it left off, and I broke another endmill. I lowered my feedrate and depth per pass, and I tried again. I made it through at least two passes before breaking the first endmill. While I had my hunk of aluminum out in the sun, I squatted down to attempt a quick pan.

I can just use smaller numbers for my 2mm endmill, right? I’m a smart guy, right? I can make an educated guess.

He told me what feed rates to use with a 1/8” endmill from Carbide 3D’s store. The first thing I did after firing up Carbide Create was head over to YouTube to see what Winston Moy thought I should be using for my settings. I broke two endmills last night! I believe it was my fault, though, and not the cheap mills!
#Shapeoko xxl free
It is on the final pocketing pass, and it will probably be working on the countour cutting operation to free the disc by the time I finish writing this blog. My emblem is cutting with one of these endmills right now. These should be sturdier, and they should cut more quickly than my 1/16” mills, so I figured I’d give them a try! That’s about 25% larger in diameter than my 1/16” endmills, and also just small enough to cut my Kestrel frames. When I was shopping at Banggood, I came across a 10-pack of 2mm carbide endmills. They get dull quickly, but everything dulls quickly when cutting carbon fiber! I’d rather dull cheap mills, right? They seem to work as well as nicer mills. I’ve been using cheap 1/16” endmills when cutting drone frames out of carbon fiber. I didn’t buy these endmills for machining aluminum. It is less detailed than the Demoman’s stickybomb emblem, and once I scaled it up enough, it looked like I would have no trouble carving it with a 2mm endmill! My cheap 2mm endmills So I decided to keep my first carve into aluminum simple.
#Shapeoko xxl how to
Even if I knew how to do it correctly, I’m not sure things would line up. I’m not smart enough to somehow combine a vcarve pass and a pocketing pass with a different bit. It only wanted to run my v-bit near the edges of the SVG. I converted a Demoman emblem to an SVG, imported it into Carbide Create, and tried to figure out how to carve that sucker out.
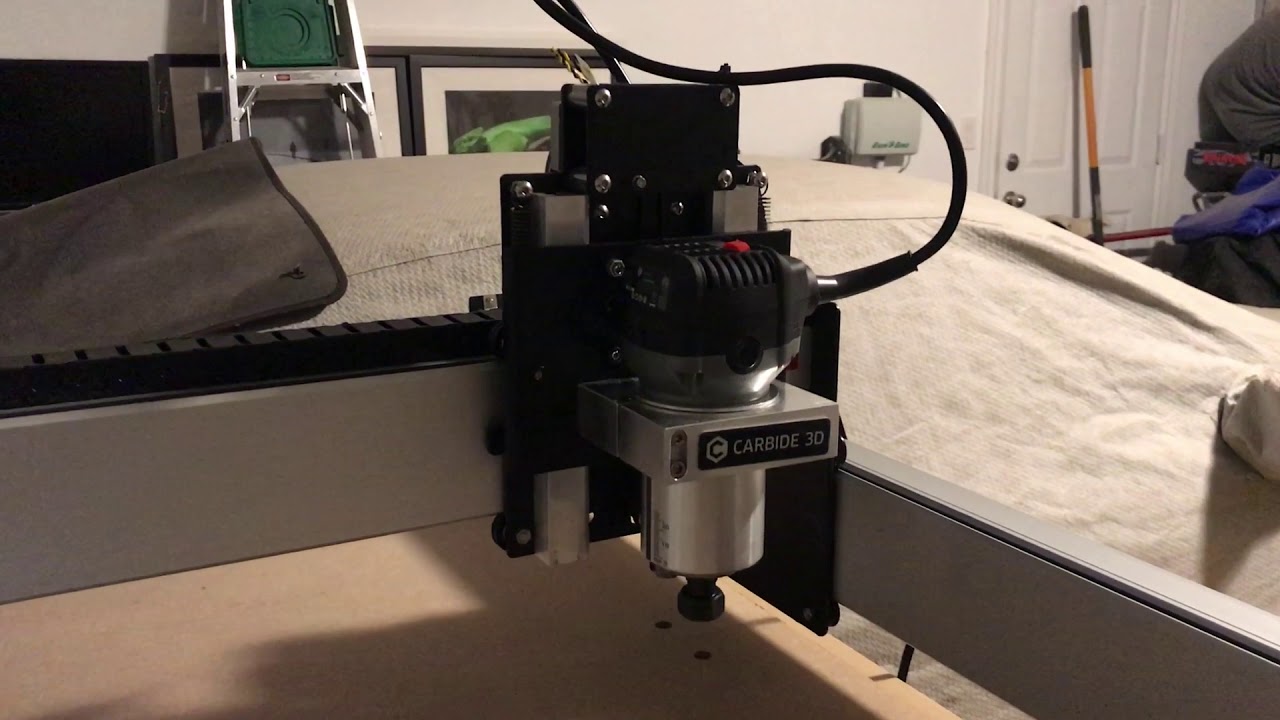
I decided to go with something simple and decorative. What sort of thing should I cut out of aluminum? The Shapeoko can handle aluminum, so I have to give it a try. I bought ¼” and ½” sheets of 6061 aluminum on Amazon last month. For now, I’m running Carbide Create using Wine. The choices in CAM software that runs on Linux are few and far between. I’m going to need to buy something better, but I haven’t decided what that will be. If you want to learn about the mistakes I’m making, then I encourage you to keep reading! I’ve broken two endmills so far thank goodness they were cheap ones! If you want to learn how to CNC aluminum on your Shapeoko, check out Winston Moy on YouTube.
